Richard Batterham dedicated his life to all aspects of making a pot. From mixing his own clay to packing the kiln, he viewed each stage as equally important for producing a good pot and was committed to the whole process of making.
While other potters might hire help to support their work or undertake some of the manual tasks, Richard preferred to work alone and completed each element of the process himself. He produced hundreds of pots every year for over 70 years and wrote meticulous lists of everything he made. Working in this way was incredibly hard work and required absolute focus and dedication to his craft, but he took great enjoyment from making pots and believed that he had been "chosen to do it".
Clay
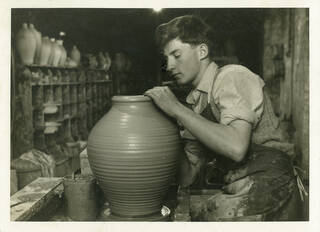
Unlike many potters today, Richard made his own clay and developed his own recipes for the clay bodies he used throughout his career. He worked predominantly in stoneware – a type of non-porous clay fired at relatively high temperatures. He prepared the clay himself in one room of the pottery where it was mixed and sieved, before being left to dry in two large beds in the pottery garden. Richard said that you can't "inject the art" at the end of making a pot, but rather, "art […] evolves from the new clay right through all the stages of making".
Porcelain
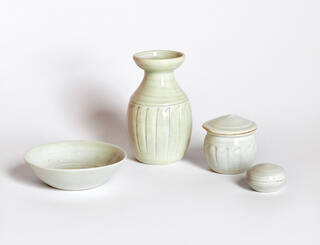
Richard worked in stoneware for most of his career. However, as he established himself as an independent potter, he briefly experimented with porcelain – a fine white clay that's challenging to work with. He first used the clay during his apprenticeship at the St Ives Pottery and most of his porcelain pots were fired in his first kiln. Richard produced a series of delicate forms in porcelain including small bottles, avocado dishes, and small lidded boxes that he described as being like "worry beads". Richard enjoyed exploring the potential of this material but preferred to work in stoneware. He made very few pots in porcelain and stopped completely in 1984.
Throwing
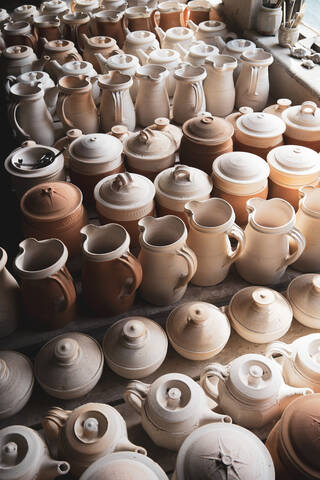
In his pottery at Durweston Richard threw all his pots on a kick-wheel, a potter's wheel worked by regularly kicking a disk at the base of a vertical shaft to keep the wheel turning at a regular pace and the desired speed. His wheel was based on the 'friendlier' and 'less mechanical' kick-wheel of the Japanese potter Atsuya Hamada (1929 – 86), whom he met and was influenced by during his apprenticeship at the Leach Pottery in St Ives.
Richard produced hundreds of pots every year and his ability to throw such a variety of forms at such pace required exceptional skill and understanding of the material. Richard made many of his forms consistently throughout his career, and by doing so he slowly refined the shape of the pot, allowing the form to subtly develop over time.
Surfaces
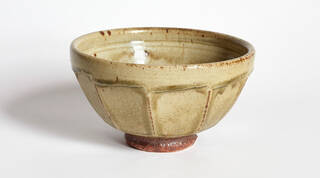
Richard did not decorate his pots, but rather applied a small repertoire of mark making treatments directly onto the surface of the raw clay before applying his distinctive glazes. This included cutting away slices of clay, creating ribs, beating, combing, fluting and incising the clay using a simple set of tools to achieve a sophisticated array of surface treatments. The dramatic cut-sided bowls demonstrate Richard's technique of cutting away slices of clay to great effect.
Glazing
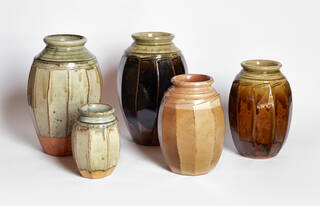
Richard described how at first he had "no experience of glazes" and had to repeatedly test different recipes to create his own repertoire of ash and iron glazes that would work on different clays and in different parts of the kiln. During firing the kiln heats up to different temperatures and so different glazes are needed for each area, as well as for the different clay bodies. These cut-sided lily jars showcase several of the glazes that Richard typically used, including manganese, ash, iron and salt glaze.
Firing
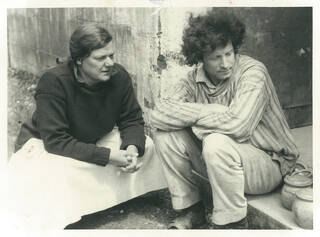
When Richard first established himself as an independent potter, he built a kiln at the bottom of the garden to fire his work. However, he soon outgrew this and built a new pottery across the road in 1966, with a three-chamber oil-fired kiln, and a fourth chamber for biscuit (unglazed) firing. Stacking a kiln on such a scale took great experience. Moveable shelves allowed pots to be stacked according to varying temperatures to achieve different effects. On average, Richard did five firings a year, and from 1968 he kept meticulous lists of every pot he made.