As peculiar as some of the pieces themselves, the language of ceramics is vast and draws from a global dictionary. Peruse our A–Z to find out about some of the terms you might discover in our incredible galleries.
.jpg)
A is for A-marked
Ceramic objects are often identified by their marks. Marks like the Chelsea anchor or the crossed-swords of Meissen are well known (and were often pirated), while the significance of others is uncertain.
One such mysterious mark is the capital A found on a rare group of 18th-century British porcelains. Once considered Italian, the group has been tentatively associated with small factories or experimental works at Birmingham, Kentish Town in London, and Gorgie near Edinburgh. The most recent theory is that they were made with clay imported from Virginia by two of the partners in the Bow porcelain factory. If so, the 'A' might refer to George Arnold, a sleeping partner in the firm.

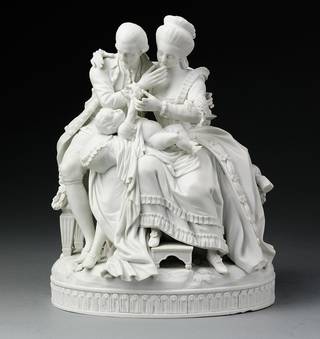
B is for biscuit
'Biscuit' comes from the French 'bis-cuite', meaning 'twice baked', although the term is most commonly used for unglazed wares that have had only a single firing. This is because the first 'baking' implied in its original usage would have been to fuse raw materials, not for firing the shaped ware.
Unless made from materials that vitrify at high kiln temperatures, biscuit ceramics are porous. To make them impervious to liquids, they require a glaze and a second ('glost') firing. But sometimes porcelain figures and ornamental wares are left in the unglazed biscuit state for aesthetic reasons.
These porcelain figures were much more expensive than glazed and enamelled versions, as there was no covering to mask imperfections. Although white, porous and difficult to clean, biscuit porcelain was fashionable for the decoration of dining tables in 18th-century France and Britain.

.jpg)
C is for China
The word ‘china’ was used in 17th-century Britain to describe porcelain imported from China. At that time Europeans were unable to manufacture porcelain, which was an expensive and highly prized material.
As the passion for collecting china intensified, greater efforts were made to discover the secrets of its manufacture. The first passable substitutes to be made in England appeared in the 1740s, and these were also called ‘china-wares’ to distinguish them from ordinary earthenwares.
Today, for many people ‘china’ is a catch-all term for ceramic tea-things, but in industrial circles it means bone china, a form of porcelain that includes bone ash in its composition.
Animal bone ash was first added to porcelain at the Bow factory in the 1740s, but its use in a hard-paste mixture was favoured by Josiah Spode in the 1790s, just as the importation of Chinese porcelain ceased to be significant.

.jpg)
D is for delftware
For most people, 'delftware' conjures up images of the blue and white pottery made in the Dutch town of Delft. The term in fact describes all 'tin-glazed earthenwares' made in the Netherlands and the British Isles. Tin-glazed earthenware, which normally has a white glaze and painted decoration, has been produced in many countries and has many different names.
Italian tin-glazed pottery is known as maiolica. It was a popular product and traded widely. By the 14th century, fleets of Venetian ships appeared in the English Channel every year, carrying cargoes of maiolica bound for England, France and the Netherlands. These ships were known as Flanders galleys, and it is doubtless from this name that 'galleyware' the original English term for tin-glazed earthenware, derives.
Although production of tin-glazed earthenware began in the Netherlands and England in the 16th century, it was not actually made in Delft until around 1600. By the late 17th century, Delft had become the most famous centre of production. Variations on the name 'delftware' have since become common in Britain for both English and Dutch pottery of this type. Wares known to have been made in the town itself are now simply called 'Delft'.

.jpg)
E is for encaustic
The term encaustic, literally meaning 'burnt in', is given to several quite different artistic processes. In ceramics it usually describes objects, often tiles, with decoration inlaid into their surface using clay of a contrasting colour. Wedgwood, however, also used the term to describe Greek-style vases with decoration painted onto their surface using coloured clay slip.
Medieval inlaid tiles were decorated by stamping the clay with a carved wooden block. The indentations were then filled with white pipe clay. In the 19th century, these tiles were called 'encaustic'. Today the term normally refers to Victorian inlaid tiles. These were made in a similar way, but instead of stamping the design into the tile, the clay was pressed into a mould with the design in relief at the bottom. Once the tile was removed from the mould, the indentations could be filled with a contrasting clay. Mechanised processes using powdered clay to form the tile body and inlaid design were also used by some manufacturers.

.jpg)
F is for flatback
This is the word used for cheap earthenware ornaments modelled only on the front and slim enough to fit the narrowest shelf. Staffordshire potters used the word 'images' for these ceramics.
In the grim and troubled mid 19th century, the working population of Britain was so hungry for folk heroes that even a small-time (but particularly vicious) 18th-century highwayman like Dick Turpin could be raised in the public imagination to the romantic status of Robin Hood. His figure was often paired with that of Tom King, another highwayman whom Turpin shot and killed by mistake. It is perhaps doubtful whether King would have wished to be immortalised alongside his killer!
Another popular hero, forgotten today, was Tom Sayers, a Pimlico prize-fighter whose bare-fist fight with the New-Yorker John Heenan at Farnborough in 1860 attracted a crowd of over 12,000. In the fourth of 37 rounds Sayers dislocated his arm, while the American was virtually blind by the time the fight was declared a draw after two hours and six minutes.
Huge numbers of these imaginary portraits were made to adorn humble cottage mantelpieces. They seem now to have a childlike charm, perhaps because they were actually made by children, who produced up to 400 small figures a day for as little as two shillings (10p) a week.

.jpg)
G is for Grand feu
'Grand feu', simply meaning 'high temperature firing', is a term especially applied to tin-glazed earthenwares (or 'faïence') made in France. It was used in contrast to an alternative method of decoration, known as 'petit feu'.
'Grand feu' decoration relied on a limited range of colours that could be painted onto the raw glaze and fired together. Often boldly painted, the result could be both highly decorative and very economical. 'Petit feu' decoration had an expensive extra enamel firing, which could only be justified when faience was attempting to rival porcelain. As tough porcelain and imported printed English earthenwares became readily available in France towards the end of the 18th century, faience declined until only reproductions and souvenirs continued to be made.
French artist potters of the late 19th century also used the term to describe stonewares or porcelains with brilliant but unpredictable red flambé glazes based on oriental prototypes. These pioneers were the first true studio potters.

.jpg)
H is for hard-paste
Hard-paste or 'true' porcelain is so-called because its raw materials and firing temperature (1200°C to 1450°C) result in a very hard, strong body that can withstand boiling water. Its other desirable qualities are whiteness, translucency, resonance and non-porosity. Its moulded details are often crisper than those in other wares.
The recipe and firing technique was invented in the 6th century in China, where there was plenty of kaolin (china clay) and petuntse (fusible feldspar rock), its two ingredients. China kept the recipe and method of production a closely guarded secret while Europe struggled to discover the ingredients. In 1709, after years of research, the physicist E.W. von Tschirnhaus and the alchemist J.F. Böttger produced hard-paste porcelain, leading to the foundation of the Saxon royal factory at Meissen in the following year. Böttger had been virtually kept a prisoner by Augustus the Strong, Elector of Saxony, until he discovered the great secret or 'arcanum'. Like the Chinese, the Meissen factory hoped to keep the secret to themselves, but industrial espionage by rival 'arcanists' led to the dissemination of this 'secret knowledge'.

.jpg)
I is for Iznik
The small rural town of Iznik nestles picturesquely on a lakeside in Western Anatolia. Here in the early 16th century an 'Imperial ware' was made for the Istanbul court of the Ottoman Sultan - the richest, most powerful monarch in Europe. European collectors in the mid 19th century thought that such fine pottery could only have been made in Persia (or Iran, as it is today). They saw the Persians as the only truly 'artistic' race of the Islamic world, and the 'artless' Arabs and Turks as barbarian nomads.
As more information became available, it was suggested that these wares were made in Damascus or the island of Rhodes, where much later Iznik ware was found. Convoluted stories explained the presence of Persian potters in these distant lands, and it was argued that 'Rhodian' wares were made by shipwrecked Persian sailors. Only in the 1920s did scholars accept that Iznik ware was Ottoman, giving due recognition at last to the Turkish potters for some of the world's most beautiful and striking designs.

.jpg)
J is for jiggers and jolleys
Machines called jiggers and jolleys are used to make tableware in ceramics factories. The derivation of these strange names is unclear, though the word 'jigger' is actually used to describe all kinds of quite different mechanical devices used in many different occupations, including billiards, golf and printing.
By the 1880s, the machines were in regular use in the potteries. Their arrival was not welcomed by the workforce. Men in particular were opposed to their introduction, but found that if they refused to work them, women were employed in their place. The two devices are similar, both consisting of a profile which is used in conjunction with a plaster mould fitted to a rotating head. This can be seen in the diagram on the left.

.jpg)
K is for Kakiemon
Kakiemon is the name given to a class of finely potted Japanese porcelains painted in a distinctive palette and repertoire of designs, which were made from the late 17th century and which have been associated with the Kakiemon family of potters. By extension it is also applied to the copies of these patterns made in 18th-century Europe, notably at Meissen, Chantilly, Chelsea and Bow.
The British versions were once thought to have been made after Meissen prototypes, but it now seems many were copied from Japanese originals. The trade in these Japanese porcelains was at its height in the first two decades of the 18th century, and many inventories contain references to 'old Japan', meaning these porcelains.

.jpg)
L is for lustre
Lustre is a very sophisticated decorative technique in which pigment containing oxides of copper and silver is painted onto a fired glazed pot. The pot is then given a low-temperature firing in which the air-supply is restricted. This produces carbon monoxide, which hungrily extracts oxygen from every available source, forming the more stable carbon dioxide. In this reducing atmosphere, the pigments are stripped of oxygen and reduced to a microscopically thin layer of metal bonded to the surface of the glaze. The lustre thus shines with metallic glints and mother-of-pearl reflections.
First seen on glass in Egypt in the 8th century, lustre production moved to Iraq, back to Egypt, then, in the 12th century, to Syria and Iran. Shortly after, it arrived in Spain, where production continued into the 20th century.
True reduced lustre should not be confused with the less demanding and more uniform industrial technique invented in the early 19th century. In the late 19th century, true reduced lustre became a passion once again among collectors and some art-potters.

-(640).jpg)
M is for Maiolica
The term 'maiolica' was used in 15th-century Italy for lustrewares imported from Spain. It is usually said that the name derives from Majorca, an island that played an important part in this trade. Recently it's been argued that the name derives from 'obra de Mallequa', the term for lustred ware made in Valencia under the influence of Moorish craftsmen from Malaga. The name was soon adopted for Italian-made lustre pottery copying Spanish examples, and during the 16th century, its meaning shifted to include all tin-glazed earthenware.
In the late 18th and 19th centuries, Italian Renaissance maiolica became increasingly popular among collectors and museums in Britain. At first it was referred to, romantically, as Raffaelle ware or Urbino ware, but soon also with the anglicised term 'majolica'.
In the mid 19th century, the term 'majolica ware' was also used by the Minton factory for their newly introduced, painted tin-glazed earthenwares. But at the Great Exhibition of 1851 Minton launched colourful lead-glazed earthenwares in neo-Renaissance or naturalistic forms called 'Palissy-ware'. Gradually the title 'Palissy' was dropped and by the 1880s the name 'majolica' was instead commonly used to describe this popular colourful ware.
In the early 1870s, the curators of the South Kensington Museum returned to the original Italian 'maiolica' with an 'i' to describe all Italian tin-glazed earthenware, doubtless to stress the Italian pronunciation and to avoid confusion with contemporary majolica.

.jpg)
N is for Nobody
Ceramic figures of Nobody combine a surprisingly ancient joke with a uniquely English pun. The joke concerns the denial of guilt: 'Who did that?' 'Nobody!' He is seen as always innocent, yet always blamed for others' deeds. Homer's Odysseus escaped Polyphemus by giving his name as 'No-man'. A medieval monk created a mock-saint (Saint Nemo) by finding all references to 'nemo' in the Bible e.g. 'Nemo deum vidit' (No-one has seen God).
In 16th-century Germany, 'Niemand' was blamed by bad servants for household breakages. Moralists took this over, arguing that individuals were responsible for the state of the Church and Society, and Protestant Reformers took this notion to England.
The pun 'No...body' is not possible in other European languages, so only ceramics destined for the British market depict a man whose legs join straight onto his head. He comes from a 1606 woodcut frontispiece to the play 'Nobody and Somebody', which Shakespeare mentions in 'The Tempest'.

.jpg)
.jpg)
O is for oxidation
In addition to changing clay into a hard ceramic material, the first firing of a pot transforms its appearance, dramatically altering colours and textures. The challenge to the potter is to control the firing conditions to achieve the desired results. The two most fundamental aspects of firing are the temperature and the amount of oxygen in the kiln atmosphere.
Altering the amount of oxygen in the kiln can result in startling effects. The very same glaze pigments may change entirely, depending on whether the kiln atmosphere is rich in oxygen (favouring 'oxidation' reactions) or starved of oxygen (favouring chemical 'reduction'). In making the pots illustrated below, the same form of copper oxide was added to the glazes. But at a critical moment during the firing of the red vase, the kiln was starved of oxygen, resulting in this rich and luscious effect.

.jpg)
P is for Palissy
Bernard Palissy (born about 1509/10, died about 1585) was a colourful and romantic character. Although patronised by the Catholic nobility, he was a militant Huguenot (Protestant) who finally perished in the Bastille. In the 19th century he was revered as both a Protestant martyr and as a master potter. In the 1850s parts of Palissy's fabled rustic grotto made for Catherine de Medici were found during excavations for the Louvre.
By using revolutionary colours, and moulds cast from actual animals and plants, Palissy had invented an entirely new type of ware. He was a great self-publicist and wrote dramatic accounts of his struggles to develop clays and glazes, an obsession that condemned his family to poverty.
His work was often copied, from the 17th century right up to the 19th century. This makes the identification of genuine Palissy wares very difficult. Unmarked Palissy-type ceramics made by unidentified workshops in the 17th and 18th centuries are sometimes designated 'school, or follower, of Palissy'. In the 19th century historicising French potters such as Charles-Jean Avisseau (1796-1861) and Joseph Landais (1800-83) made and signed similar wares.

.jpg)
Q is for Queen's Ware
Cream-coloured earthenwares, containing a combination of whitish clays and calcined flint, were made in Staffordshire from the 1740s. Josiah Wedgwood - whose extraordinary skills as a ceramic technologist were very nearly matched by his talents as a salesman and entrepreneur - made various improvements to the material during the 1760s.
Following his appointment as Potter to Queen Charlotte in 1766, he named his improved creamware 'Queen's Ware'. This did much to ensure the fashionable status of his pottery. But as the term rapidly became the generic name for creamware, it was also widely used to promote the products of his competitors. Along with transfer printing and the bone china formula, creamware was one of the major technical advances in ceramics that the British can lay claim to.

.jpg)
R is for repairers
The 'repairers' working in the 18th-century British ceramics industry did not, as their name suggests, mend or rivet broken ceramics. Rather, they were the skilled craftsmen responsible for assembling figures and certain wares from the constituent parts formed in plaster piece-moulds. They also cleaned up mould seam-lines, incised or sharpened up such details as facial features and clothing accessories, and added small hand-modelled or separately cast components.
Repairers were responsible for many of the variations found in sculptural porcelain pieces, as here. Modelling and designing appear to have been overlapping areas of activity in the 18th-century ceramic industry; but in assemblages of this type - which can bring together thrown shapes, standard moulded components, hand-pierced work and parts modelled by hand - the distinctions between modelling, repairing and designing become completely blurred.

.jpg)
S is for slip
'Slip' is clay suspended in water to form a liquid of creamy consistency. Many 'industrial' and modern ceramics are formed entirely from slip poured into plaster moulds.
Since around 1900, however, the term 'slipware' has been applied specifically to slip-decorated ware. These are pots that have been coated in slip, have applied slip decoration, or a combination of both. The clay used for the slip is usually in a contrasting colour or colours to that of the ceramic body. Slip decoration comprises a variety of techniques such as painting, trailing or 'jewelling' or inlaying into relief designs.
By applying one or sometimes two coats of slip, the potter can decorate the pot in various ways. Incision (also known as 'sgraffito') involves cutting through the slip to reveal the body beneath. Combing or feathering means dragging a serrated tool through the wet slip coats. Marbling is created by agitating the still-wet, slip coats on the object.

.jpg)
T is for Transfer printing
Transfer printing is a way of reproducing two-dimensional designs on ceramics. At its best it results in high-quality decoration at a low cost per unit. The design is printed onto a sheet of tissue paper or a thin pliable layer of gelatin (animal glue), and then transferred onto the surface of the ware.
The technique was in use at Birmingham in 1751, though it appears to have been practised at the Doccia factory near Florence in the previous decade. 18th-century transfers were made from both paper and pliable sheets of animal glue (or gelatin), but only paper transfers could be used for printing 'blue and white wares'. During the 19th century gelatin transfers were superseded by tissue paper. This type of work is best exemplified by the familiar Willow Pattern.

.jpg)
U is for underglaze
Underglaze is the opposite of overglaze. It refers to ceramic decoration that lies under the glaze, which forms a protective layer. The technique only became possible in Europe when biscuit firing was introduced for fine earthenwares and porcelain (see B is for biscuit). Only a few pigments could withstand the heat of the glaze firing.
The toughest and most reliable underglaze colour proved to be cobalt blue, used by the Chinese potters from the 14th century. In England, blue painting on porcelain was soon largely replaced by transfer printing. This was less skilled work, and required less labour, so provoked a strike among worried factory decorators in 1770. Happily, the technique was then applied to cheaper earthenwares with such success that the pottery industry rapidly expanded.
The decoration on 'Tortoiseshell ware' is also under-the-glaze, produced either by applying metallic oxides with a sponge or brush directly onto the biscuit body, or perhaps with clay slips stained with oxide colours.

.jpg)
V is for Veilleuse
This unusual device derives its name from the French for a night vigil. It was used to keep a drink or portion of semi-liquid food warm at night-time, initially only at the bedside of infants or invalids, but from about 1800 for more general use. In the days before electric timers, it was the nearest thing to a combined 'teasmade' and nightlight.
It consists of a hollow pedestal with pierced vents surmounted by either a covered food bowl or a small teapot. The heat source is oil burned by means of a floating wick, located in a tiny bowl in the bottom of the pedestal. Veilleuses were made in tin-glazed earthenware, creamware, stoneware, porcelain and bone china. They were chiefly made between 1750 and about 1860.

.jpg)
W is for wasters
Wasters are the discarded remains of ceramic objects that became damaged or deformed during firing. They provide us with first hand information about production processes. Quite often, the small supports called 'spurs' on which a pot was fired are fused to the glazed surface and sometimes we find a whole stack of dishes, collapsed and fused together. When excavated in their original, workshop context, wasters also help us to link certain wares to specific production centres.
Wasters are rarely recycled by the pottery workshops. Instead, they are often used as hardcore or ballast. Huge quantities of British pottery wasters were employed in the building of streets in New Delhi in the 1920s. Wasters should not be confused with slightly deformed products, which often still find their way to consumers as 'seconds', although such pieces have often misled scholars.

.jpg)
X is for Xanto
Francesco Xanto Avelli of Rovigo is the most famous decorator of pottery of the Renaissance, but also the most enigmatic. A literary man, working for most of his career in Urbino, Xanto specialised in 'istoriato' maiolica, a style in which the whole surface of a plate or pot was covered with a painted scene. He often derived his figures from prints, combining them to form his own compositions.
Between 1530 to 1542 Xanto signed many of his works. In 1530, he was part of a group of maiolica painters in Urbino who demanded higher wages from their patrons. The workshop owners responded with a blacklist of painters, who could only be employed at set fees and with general approval of all patrons. It is likely that this incident prompted Xanto to sign his works in full. There has been much speculation about Xanto's work before 1520 and various groups of 'istoriato' maiolica with different marks have been attributed to him.

.jpg)
Y is for Yellow Ware
Yellow Ware or Yellow-glaze Ware are terms usually applied to Staffordshire earthenwares of the period 1800-40, often with transfer-printed or silver lustre 'resist' decoration over a bright yellow glaze. In recent years these have become exceedingly popular with American collectors, who reintroduced these terms.
Earlier, the same names had been used to refer to buff- or cream-coloured ware, and to common earthenwares covered partly or wholly with a yellowish glaze, as well as to American ceramics made from a yellow-coloured clay. However, contemporary manufacturers - notably Josiah Wedgwood, who perfected a type of yellow glaze in the 1750s - never used such terms.
The first European porcelains with a solid yellow ground colour were highly prized. At Meissen in the 1720s, yellow was used for grand porcelain vases made for Augustus of Saxony. Significantly, it was also the very first ground colour to be perfected at the Vincennes/Sèvres factory, in 1751. In England, apart from occasional use at Derby and Pinxton, the desirable colour was only applied successfully to highly decorative mass-produced earthenwares.

.jpg)
Z is for Factory Z
Factory X, Y and Z were classifications given to three groups of late 18th-century English porcelains formerly attributed to the New Hall factory in Staffordshire. Following detailed comparative analysis of their potting and decoration, collectors established that they were made at other, as then unidentified works, even though they were dependent on New Hall's innovations in technique and derived in part from New Hall's patterns and shapes.
Further unattributable groups of this type have been discovered since the original trio were first identified in print in 1971. Indeed, one authority has suggested that collectors and connoisseurs could just as well have started at 'A' and worked through the alphabet in attempting classification of these problematic wares. Since then Factory X has been identified as the Tunstall works of A. & E. Keeling, but Factory Z is still a puzzle.