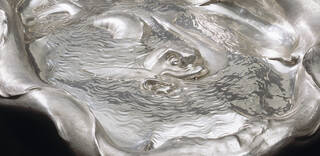
An A–Z of metalwork
An A–Z of metalwork
Discover some of the quirky, ingenious, dangerous and dramatic objects in the Metalwork collection in this A–Z
Metalwork permeates every aspect of our lives, from the kitchen utensils we use daily, the railings and lamp posts that line our streets, the components in our phones, to the heirlooms we cherish for life. The V&A holds one of the world's largest and most varied collections of Metalwork with around 45,000 objects from the Bronze Age to the present day. Additionally, the Gilbert Collection of gold, silver and micromosaics on loan to the V&A shows spectacular items including Frederick the Great's diamond-encrusted snuffbox.
Read more Read lessAn A–Z of metalwork
Discover some of the quirky, ingenious, dangerous and dramatic objects in the Metalwork collection in this A–Z
Dressed to kill – fashion and armour
Discover what the fashion-conscious Renaissance man would have worn on the battlefield or for jousting
Unlocking a 17th-century strongbox: ASMR
Peek into the past as we look inside a historic strongbox
Archibald Knox, Liberty and the Celtic Revival style
Discover a master of metalwork
How was it made? Electrotype
Discover how a metal copy of an object is created
How was it made? Silver watch case
See how an 18th-century watch case is made
Conservation of the Poynter Room grill
See the magnificence of the metalwork return
How was it made? Guilloché enamelling
Watch precise geometric patterns appear on metalwork in this centuries-old process
Serving up: silver slices
Contemporary silversmiths respond to a unique, creative brief to redesign the humble fish slice.
How was it made? 3D scanning and printing
See how 3D scanning and printing techniques are used to reproduce an object from our collection
Laying a wacky and whimsical Christmas table
How wacky is your Christmas table? Discover some of our favourite festive fare, with a twist
A history of jewellery
Explore jewellery techniques and designs from the bronze age to the modern day illustrated with key pieces from our jewellery collection
Rosalinde and Arthur Gilbert and their collection
Meant ‘for everyone’, the Rosalinde and Arthur Gilbert Collection comprises gold and silver, enamel miniatures, gold boxes and mosaics
Biscuit tins – a bite-sized history
Novelty biscuit tins in all shapes and sizes
The gold ewer
Read about the restitution of a 4,250-year-old Anatolian gold ewer
Teapots through time
Discover some of the finest examples of teapots produced over the last five centuries
How was it made? Champlevé enamelling
See how this medieval technique was carried out
Deconstructing samurai armour: ASMR
Removing the helmet and untying intricate knots – watch as the 18th century piece is dismantled
Dressing a 17th-century dolls' house: ASMR
Step inside a tiny dolls' house