The V&A Conservation department preserves, conserves, investigates and facilitates the display of the museum's collections. Combining expert knowledge of materials and techniques with outstanding practical skills – underpinned by scientific analysis and research – we evaluate the condition, provenance and authenticity of our collections, helping to safeguard them for future generations.
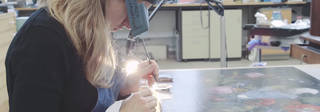
Who we are
The department includes specialists in the conservation of textiles and dress, ceramics and glass, stained glass, metals, sculpture, furniture and frames, paper, books and paintings. Our team of conservation scientists use traditional techniques and modern methods of analysing the collections, promoting knowledge and understanding of museum objects and their environment. Conservation teams also help the museum to find new and innovative ways to store and display its collections and to establish the safe transit of objects when on loan or touring. This expertise is shared with colleagues around the world through collaborations with other institutions, and by offering student placements in the department.
Tel: +44 (0)20 7942 2000
Email: conweb@vam.ac.uk
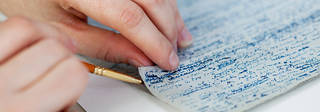
Conservation stories
Our engaging film series follows a selection of the most challenging and fascinating conservation projects – from the treatment and redisplay of the delicate costume worn by Julie Andrews in My Fair Lady, to the stretching of a huge Bollywood film hoarding.
Keep up to date with the latest archive finds, day-to-day conservation and collection management stories, news and projects in this dedicated section of the V&A blog.
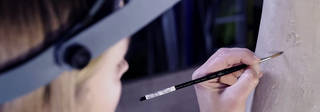
Jobs and training opportunities
Jobs and training opportunities, when available, are posted on the V&A jobs page:
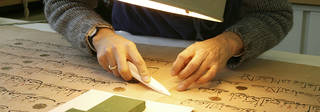
V&A Conservation Journal
Published annually since 1991, the Conservation Journal is our informal publication for anyone interested in the conservation of our cultural heritage – from conservation professionals, to students, and staff of museums and cultural bodies. Topics range from the technical study of historical objects, to new methods and materials, preventative projects, and the installation of new galleries. Recent editions can be found via our blog, while a back-catalogue of the Journal is available via the link below.
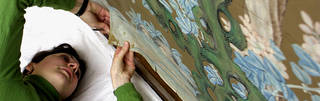
Caring for your possessions
Want some guidance on how best to look after your objects and artefacts at home? The Institute of Conservation has a wealth of practical online resources written by conservation experts.