Conservation Journal
Summer 2005 Issue 50
The Castellani diadem
The Jewellery Gallery of the Victoria and Albert Museum is currently undergoing complete refurbishment. This work has created an invaluable opportunity for staff and external specialists to conduct in-depth study and analysis of materials and techniques used in the manufacture of jewellery from Ancient Egypt to the present. It is hoped that the redisplay will incorporate up to four and a half thousand objects, including some which were previously not in a displayable condition. A gold, enamel and pearl diadem (640-1884) designed by Alessandro Castellani is one such example.
Alessandro's father, Fortunato Pio, founded the firm of Castellani in Rome in 1814. Towards the late 1830s Fortunato Pio began to study the ancient jewellery making techniques he had observed in Greek and Roman archaeological objects. The work produced was extremely fine. This work was further developed by his two sons, Alessandro and Augusto.
The design for the diadem, by Alessandro Castellani, is believed to have been closely based on the 'Palo' diadem, an ancient Greek artefact believed to have been found at Cumae, Italy (now in the Louvre, Paris). There are only five known versions of this work, each having variations in design.1

Figure 1: The diadem shortly after acqisition (neg. 25341). Photography by V&A Photographic Studio, pre-1903 (click image for larger version)
The diadem was acquired by the Museum from a sale of Castellani's effects in 1884. A photograph taken before 1903 (Figure 1) shows the diadem as complete and in good condition. However, after the picture was taken, the condition of the diadem was dramatically altered: the thin gold tube which forms the base/frame had been straightened, there were two complete fractures and two repaired fractures (with adhesive) along its length. Some of the decorative panels were also crooked and had a number of their tips and flowers crushed (Figure 2). There are no Museum records of how or when the damage occurred.
Richard Edgcumbe, Senior Curator in the Metalwork Collection, requested that the diadem be examined with a view to returning it as near as was possible to the original state. Factors taken into account at this point were: the lack of structural stability (the various broken parts were free moving and were causing unavoidable damage through handling); in the current condition, the diadem couldn't convey to the visitor a clear understanding of its function; although a very long time ago, the damage had been incurred while the diadem was in the care of the Museum, and as such it was felt we had a duty to return the diadem to the form in which it was acquired. It was decided that the benefits of restoring the diadem outweighed the risks.
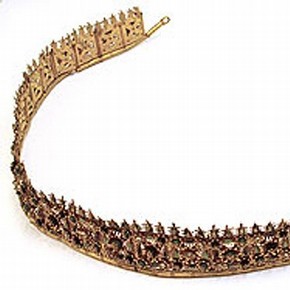
Figure 2: The diadem before treatment. Photography by Joanna Whalley (click image for larger version)
In this instance, a jeweller might consider removing the panels, annealing the tube (heating to allow the crystals in the metal to redevelop and so make the tube more flexible and less likely to fracture when being reshaped), and soldering the damage already incurred. This could not, of course, be considered in this case. The process involves high temperatures and therefore there are a number of inherent risks, particularly with thin tubing. It would also permanently alter the crystal structure of the metal which might affect any subsequent research into Castellani's manufacturing techniques. A more conservative approach was obviously required.
The early photograph of the original form was studied and a template of the base of this form was drawn. The diadem was placed over the template and the separate parts were aligned as closely as possible to the shape. The tube was then very slowly and gently eased back into the curved form.
The old adhesive repairs to two of the fractures in the tube frame were checked: there was an excess of what appeared to be epoxy resin around the joints. The excess was removed mechanically under magnification and retained for FTIR analysis.2 The repairs appeared to be stable and strong, and so were left in place: the strong solvents necessary to remove this adhesive may not penetrate the join properly and could possibly create long term problems if they were not successful. Should the adhesive fail in the future then access to the interior will be afforded and the adhesive will be removed and replaced more safely.
The next step was to repair the two open fractures in the tube frame. The fractures had occurred in areas which are vulnerable to further damage from flexing in many directions. The choice of repair had to provide a great degree of support in response. An internal armature was made (from gold) which should prevent any movement around the join from affecting the join itself (Figure 3). Ideally the adhesive selected should be easily reversible, and Paraloid B-48N (methyl methacrylate/butyl acrylate copolymer) seemed most suitable. However, on application the join proved relatively air tight and the solvents in the adhesive couldn't evaporate fully to allow it to set properly. There were also general reservations about its relative strength. As a result, a 2-part epoxy resin was used for the repair. The new and old repairs were partially disguised using fine gold powder dusted onto a weak solution of Paraloid B72 (ethyl methacrylate/methyl acrylate copolymer) in toluene and Industrial Methylated Spirit (IMS).
he distorted decorative panels were straightened, the gold here had not been work hardened and was still very soft. Where there were extreme distortions to the applied leaves and petals, these were reshaped in the same way.Once the diadem was structurally stable, it was possible to clean it. This was done using IMS. The enamels appeared to be chemically stable and so they were also cleaned using IMS. There were fine fractures to three small enamels where the gold panels had been allowed to move freely before the tube was repaired, these were consolidated using a weak solution of Paraloid B72. The pearl beads were cleaned with deionised water (Figure 4). Finally, a closely fitting mount was made in brass with Plastazote‚ to provide gentle and even support (Figure 5).
The diadem was recently included in the exhibition 'Castellani and Italian Archaeological Jewellery' at the Bard Graduate Centre in New York, transferring to Somerset House, London, 5 May to 18 September 2005.
The newly refurbished Jewellery Gallery will reopen at the beginning of 2008. The display will explore and present all aspects of jewellery making techniques and materials through the V&A's exceptional collections.
References
1. Weber Soros, S., Under the Great Canopies of Civilization: Castellani Jewellery and Metalwork at International Exhibitions, in 'Castellani and Italian Archaeological Jewelry', Yale University Press (2004)
2. Keneghan, B., Polymer Scientist, Science Department, V&A. The adhesive proved to be an epoxy resin mixed with a small amount of an unknown material.
Suppliers
Plastazote®, Polyformes Ltd, Cherry Court Way, Stanbridge Road, Leighton Buzzard, Bedfordshire,
LU7 8UH
Summer 2005 Issue 50
- Editorial
- Rising damp - a history of the Conservation Department
- V&A Conservation on the world wide web: a secondment to the V&A web team
- The ethics checklist - ten years on
- Plastics preservation at the V&A
- Working for Diaghilev
- Pugin's wallpapers from The Grange
- Prevention is better than the cure
- Research
- The Castellani diadem
- In pursuit of a clear answer: An Exhibition Road partnership
- Investigation of the room temperature corrosion of replica museum glass
- Professional collaboration - the Prince of Wales Museum of Western India
- V&A/RIBA partnership
- Picture and mirror frames: Reflections on treatment past, present and future
- A simple solution?
- Appendix 1: Victoria & Albert Museum Conservation Department Ethics Checklist
- Conservation of a tortoiseshell book cover
- The hand that rocks the cradle: Conservation administration, present and future
- Printer friendly version