Conservation Journal
Summer 2006 Issue 53
Harpies - past and present
Amongst the 47 textile objects chosen for the new Jameel Gallery of Islamic Art there were a proportion that had been treated in the past. There were those that had been displayed in the old gallery or elsewhere in the Museum and others that had been requested for loan. Each object was assessed with regard to the new design requirements and the estimated duration of display. Some of the past treatments proved robust and very little or no extra work, other than a new mount, was needed. In other cases failings came to light. There was also the odd treatment that altered our perceived prejudices.
An object known as the Harpies (T.399-1980) was a good illustration of all three. Its past treatment, though robust, had failings that could now be recognised as methods and materials have advanced. It also utilised a technique that has a slightly ambiguous reputation but which had served the object well.
The Harpies is a fragmented piece of exquisitely woven silk double cloth (approximately 1.8m x 0.5m) depicting large human headed birds or harpies (Figure 1). It was excavated in the 1920s from a burial site in Rayy, Iran and dates from around the eleventh century. The desiccated silk is now extremely friable and subject to powdering. There are remnants of what appear to be linen body wrappings adhering to the verso.
The piece was treated when it was acquired by the Museum in 1980. It had been lightly adhered to a silk covered, padded board using dots of carboxymethyl-cellulose (CMC) adhesive around the edges of the fragments. The object was then framed and glazed, utilising the weight of the glass to hold the bulk of fragments in position.
Although the fragments appeared well supported and their general condition had not obviously deteriorated, there were several points that needed to be considered before the piece could be re-displayed:
- the gallery designers' request for a metal frame - to better integrate the object into the new gallery
- the heavy weight of the thick glass bearing down on the object, its breakable nature and the inferred danger to the object
- the insufficient padding of the existing board
- the use of unsealed wood as a backboard and the current availability of more inert and potentially less harmful support materials
- the method of framing. As it was only the pressure of the glass holding much of the object in position, its removal would leave the object extremely vulnerable.
All of the above could be addressed with a new pressure mount using updated techniques and materials.
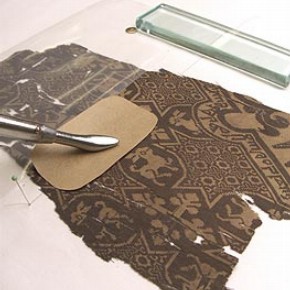
Figure 2. Sticky threads being heat-set to the verso of the object. Photography by Natalia Zagorska-Thomas (click image for larger version)
What are 'sticky threads'? To create them, sections of fine thread are passed through a pool of thermoplastic adhesive mixed with water, forming rivulets of glue along its length. When dry the sticky threads can be applied across a textile's surface, using heat or solvent vapour for reactivation. This treatment is characterised mostly by its limitations. It does not impart any strength because of the minimal surface area of contact between the thread and textile. Therefore it can not be used to produce a self-supporting joint between separate fragments. The scant contact means that if any stress is exerted on the bond, it will quickly fail. When used on the obverse of an object, the threads sit on the surface, making them unsightly.
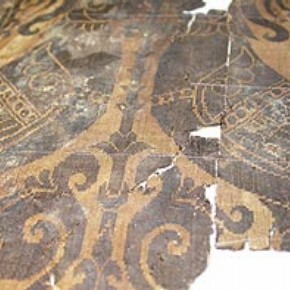
Figure 3. Sticky threads holding textile fragments in place. Photography by Natalia Zagorska-Thomas (click image for larger version)
The object was carefully realigned whilst laying face down. A decision was made to replicate the sticky threads using fine polyester Skala thread and the thermoplastic adhesive Vinamul™ 3252 (vinyl acetate -ethylene copolymer). The threads were laid across the verso of the object at regular intervals and set in place using a heated spatula (Figure 2). They not only held the fragments in position but also prevented sections floating away on air currents in the Studio whilst the treatment was in progress (Figure 3). In addition, if the piece requires re-glazing in the future, the threads should counteract the effects of static electricity during removal of its Perspex® cover.
The piece was mounted on a lightweight, rigid board, Hexlite® 620, padded with (a recently tested) needled polyester and cotton domet, and covered in dyed silk. A sheet of acrylic was screwed down over it, firmly but not tightly. It was then framed in the requested metal frame, with a secondary glazing of UV filtered acrylic. If the outer acrylic becomes damaged or a different frame is requested, the exterior package can be dismantled without disturbing the pressure mounted inner unit.
The Harpies is one of 47 differing textile objects in the new gallery. Assessing and preparing objects for a project of this scale is always an education. It gives us the invaluable opportunity to review and evaluate past and present methods whilst keeping an eye on the future.
Materials
Hexlite® 620 (Hexcel Composites Ltd, Duxford, Cambridge, CB2 4QD)
Vinamul™ 3252 (Celanese Emulsions, De Asselen Kuil 20, 6161 RD Geleen, NL www.celanese.com)
Summer 2006 Issue 53
- Editorial
- Developing the Islamic Middle East gallery and touring exhibition
- Planning the packing for a touring exhibition
- The traveling technician - the role of a technician as courier
- Harpies - past and present
- Tiles from the tomb of Buyanquli Khan
- Pigment analysis of a Persian album page
- Collaborative investigation of the Eltenberg Reliquary
- Frankfurt Kitchen: patina follows function
- Printer friendly version