Conservation Journal
Summer 2006 Issue 53
The traveling technician - the role of a technician as courier
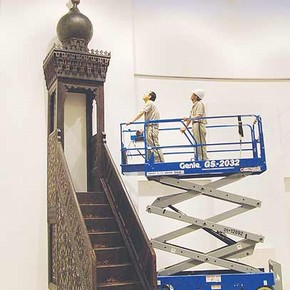
Figure 1. The Minbar (1050-1869) during installation. Photography by Phil Sofer (click image for larger version)
In recent years there has been a continued increase in the number of loans from the Museum to exhibitions in the UK and around the world. The Museum exhibition program has also expanded and it is not unusual for there to be three or more V&A exhibitions travelling the globe. It is standard practice at the V&A for a representative of the Museum to act as courier during the movement of objects between locations. A courier is responsible for the safety of the object(s) during all stages of transport between venues and must supervise the unpacking (or packing), installation (or de-installation) and check the objects against condition reports provided by V&A conservators. As staff in the Museum continue to develop conservation and packing techniques, objects that would have previously not traveled, due to conservation issues, size or complexity of packing or installation, can now be included in exhibitions. This brings new challenges for the museum courier. In some situations there can be an advantage in sending either a conservator or a technician as that courier.
The recent touring exhibition 'Palace and Mosque' illustrates the issues involved and the benefits of including a technician as courier, and how their role differs from that of other V&A staff. 'Palace and Mosque', which travelled to four museums on three continents, included some of the finest objects from the V&A's Islamic, collection. The object list included a Minbar, a mosque pulpit with an overall height of 7 metres (Figure 1), a large ceramic fireplace, two large carpets and numerous fragile objects with specific handling and installation requirements. With these challenging objects and short installation/de-installation windows at some venues, a team of four couriers was put together comprising of the project coordinator, a curator, a conservator and a technician. The advantage of including a conservator and a technician is that they can be selected from staff who have worked on the conservation, installation/de-installation, and packing of the objects at the V&A, and so bring with them valuable knowledge of specific objects.
The 120 objects were packed in 50 crates and split into two shipments. The accompanying article 'Planning the packing for a touring exhibition' by Richard Ashbridge discusses the organisation involved in this. The crates were transported between venues by air and by road. Space is often tight on a cargo plane and it is often impossible to avoid stacking crates when palletising. All V&A couriers are trained to make decisions under these circumstances, however the 'Palace and Mosque' crates were unusual in their size and weight and transporting them was complicated. As technician couriers are equipped with the knowledge of crate construction and packing methods they can confidently make decisions as to which crates can safely be stacked. This knowledge is also helpful when loading and unloading trucks as it is important that the weight is sensibly distributed and the crates properly secured. The seven metre high Minbar (1050-1869) would be complicated to install, however the initial challenge was to get the crates to the venue! Due to the size of the object it had to be transported in smaller sections. The two largest crates contained the fragile sides of the Minbar, they were 3 metres tall, 4.5 metres wide and tipped the scales at 750 kg each. It helped to have a technician on hand with the knowledge to inspect slinging methods and instruct on the safest way to move crates of this size and weight. Figure 2 illustrates the loading of these crates onto a truck in Japan. The narrowness of the crate made it unstable, so all movements had to be carefully controlled.
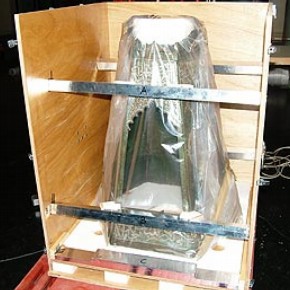
Figure 3. Crate containing the brass mosque lamp holder (109-1888). Photography by Phil Sofer (click image for larger version)
With all V&A loans, a courier is equipped with detailed conservation reports, packing notes and photographs and will usually be briefed by the V&A Packing and Transport team on how to unpack and repack an object. At each leg of the 'Palace and Mosque' tour the V&A technician worked with local technicians to lead that team in the unpacking/packing and installation/de-installation of the more challenging objects in the exhibition, as well as being on hand to help the other couriers with any packing or installation queries. It was vital to have a V&A technician to lead the installation of an object such as the Minbar. The components had to be installed in a very specific order that required a coordinated team of eight technicians and numerous pieces of equipment. In Figure 1, the Minbar is shown during installation in Japan before the addition of the elaborate door frame and doors at the foot of the steps. A technician is inspecting the finial, having just secured it against possible earthquakes.
Some objects in 'Palace and Mosque' required specific climatic conditions that had to be tightly controlled both on display and during transit; an example of this is a brass mosque lamp holder (109-1888) that had to be kept below 30% rh to ensure areas of old corrosion would stay inactive. Following consultation with Conservation, a crate was designed to control the environment (Figure 3). The object was sealed in a micro climate, maintained through a combination of silica gel and molecular sieves to remove excess moisture from the air. The size and weight of the object dictated the use of a wooden crate so this was treated to prevent off-gassing. The object sits on an acrylic base within the packing which, is designed so that the lamp can be installed without directly handling its fragile surface. The technician's familiarity with both packing and installation methods ensured that the object could be transferred between the protective atmospheres of the crate and display case in the minimum period of time, reducing its exposure to higher humidity levels in the gallery. It was also vital that the object was repacked in exactly the same way each time, to ensure that the object's condition remained stable.
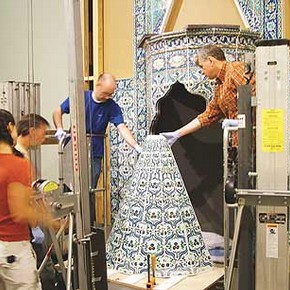
Figure 4. Installation of the Iznik fireplace (703-1891). Photography by Phil Sofer (click image for larger version)
Acting as a courier also provides opportunities to share information with technical staff from other museums. A good example is the installation of the Iznik fireplace (703-1891) shown in Figure 4. Following conservation treatment the object was mounted into manageable sections for transport which ultimately fitted together onto an aluminium support structure for display. Although an installation method was devised before the object left the V&A, the first time the fireplace was constructed in its new configuration was when it reached the National Gallery of Art in Washington DC. This was an opportunity (since there was no tried and tested method of installation), to discuss, develop and improve methods with technical staff at each venue and to plan for the object's eventual installation on return to the V&A.
As we have seen there are many advantages in choosing a technician to act as a courier, particularly when dealing with complex objects that are difficult to install or that require specialist packing and transport. The technicians' primary concern will be the welfare of the objects, in addition by working at different venues in the UK and worldwide there is the opportunity to build relationships with other technical departments and exchange ideas which benefit the individual, Technical Services and the Museum as a whole.
Summer 2006 Issue 53
- Editorial
- Developing the Islamic Middle East gallery and touring exhibition
- Planning the packing for a touring exhibition
- The traveling technician - the role of a technician as courier
- Harpies - past and present
- Tiles from the tomb of Buyanquli Khan
- Pigment analysis of a Persian album page
- Collaborative investigation of the Eltenberg Reliquary
- Frankfurt Kitchen: patina follows function
- Printer friendly version